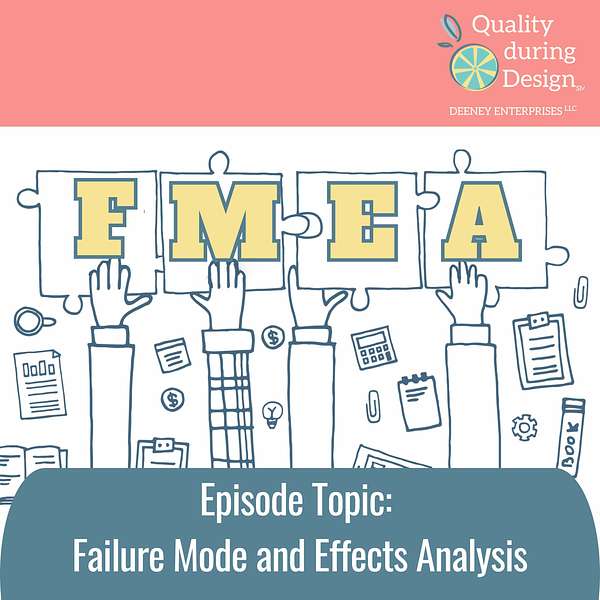
Quality during Design
Quality during Design is a production of Deeney Enterprises, LLC. It is a podcast for product designers, engineers, and anyone else who cares about creating high-quality products. In each episode, we explore the principles of quality design, from user-centered thinking to iterative development. We introduce frameworks to make better design decisions and reduce costly re-designs. We explore ways to co-work with cross-functional teams. We also talk to experts in the field about their experiences and insights.
Join host Dianna Deeney in using quality thinking throughout the design process to create products others love, for less. Whether you're a seasoned designer or just starting out, looking to improve your existing designs or start from scratch, Quality during Design is the podcast for you.
Quality during Design
Decoding FMEA for Product Complaint Investigation
Who wouldn't want a treasure trove of product knowledge right at their fingertips? We explore FMEA (Failure Mode Effects Analysis) and unlock its potential for complaint investigation. Harness the power of FMEA - not just a tool, but a wellspring of team knowledge about your product.
But we're not finished there - we're turning FMEA data into actionable knowledge. We delve into the use of FMEA for field failure investigation and innovation. We'll dissect the various components of FMEA, showing you how they can be used to evaluate data and investigate causes.
Come with us as we turn information into knowledge, and then innovate with FMEA.
This is a Quality during Design Redux episode, originally "How to use FMEA for Complaint Investigation". Visit the podcast blog, here.
**BI-WEEKLY EPISODES**
Subscribe to this show on your favorite provider and Give us a Rating & Review to help others find us!
**ONLINE COURSE**
FMEA in Practice: from Plan to Risk-Based Decision Making is enrolling students now. Nearly 300 students have taken this course. Join them to start your FMEA journey or take your skills to the next level. Click Here to get started.
**MONTHLY DIGEST**
Subscribe to the free monthly e-newsletter: newsletter.deeneyenterprises.com
Get the short version on Linked-In: Subscribe here.
About me
Dianna Deeney is a quality advocate for product development with over 25 years of experience in manufacturing. She is president of Deeney Enterprises, LLC, which helps organizations optimize their engineering processes and team performance by promoting the use of reliability and quality methods during design. She offers consulting services for managers and directors, training for engineers through the Quality During Design program, and other practical resources.
Hi, it's Dianna Deeney. These last few weeks on the Quality During Design podcast, we've been talking about reliability during design. We started with reviewing ways to manage risks during a design process. And then we've been talking about how to work with reliability engineers during design, the value they can bring and the contributions that they make to design. No matter our best intentions and our best efforts, we strive to make a product that is going to be reliable and is going to work and be a success in the field, but there is the reality that failures are going to happen in the field. When we acknowledge that we can understand that this is more data and information in order for us to make decisions, we investigate the complaint and figure out the root cause of it. From that complaint information, we can make some decisions. We may need to make some business decisions and determine if this is something we need to act on, and this information is also great for design inputs for next iterations or for other products. If we designed with a failure mode effects analysis, an FMEA, we might be able to use that to help us with our complaint investigation and to help us determine the root cause and make some of these decisions based on risk. To explore this further within our reliability during design series, I'm pulling another episode from the archive. It's called How to Use FMEA for Complaint Investigation. We stepped through an example of how to do it and what you can do with FMEA after your products already in the field. So, without further ado, here is the Quality During Design Redux episode. Enjoy.
Dianna Deeney:We're new to a product line and our team is asking for our help in addressing field complaints. They've identified a trend and want our recommendations on what to do to fix it, but we don't know the history of the product and we're barely familiar with all the bells and whistles it contains. Where do we start More after this brief introduction? Hello and welcome to Quality During Design, the place to use quality thinking to create products. Others love for less. My name is Dianna. I'm a senior level quality professional and engineer with over 20 years of experience in manufacturing and design. Listen in and then join the conversation at QualityDuringDesigncom.
Dianna Deeney:Fmea, or Failure Mode and Effects Analysis, is a tool we can use to help us investigate complaints from the field or field events. Even if it was done during design and not touched since, we can use it, it's the collective team knowledge about the risks of this product, so it's a valuable source in our investigation about what's going on in the field. We've got a problem. We might have several problems. The first thing that we do is we consider do we have data about the problem Or do we have complaint data about a symptom? Is our complaint team giving us trends of data that are really symptoms? Symptoms are signals that something's wrong. It's what we notice is wrong. Having an ache in our shoulder is a symptom. The problem may be any one of several things that we've damaged the rotator cuff or we're developing arthritis in the joint, or maybe we just pulled a muscle. The staff that is investigating complaints and trends may be trending based on symptoms, in which case we may have several different problems that are contributing to one symptom. If this is the case, then we can get a start on our investigation by using the FMEA that's on file for the product. We'll want to check the FMEA for the symptom that's happening. Likely they'll be in the effects column, where we find the effect listed. What are the types of failures associated with it? We'll still need to do further investigation into the complaint data or hopefully we have some product that we can look at, study or test. That's getting to the problem.
Dianna Deeney:If our complaint handling staff is performing investigations to determine the cause of the complaint and their trending on the problems, then we're likely going to be able to look at the FMEA from its failure column. We match up the FMEA failure with what the complaint team is finding as the problem and ensure the effect column on the FMEA matches up with the details of the complaint. From the effects and failures we can then start looking at the causes. We're casting a net with the causes but then we're going to use the FMEA more to whittle down the likely culprit. What causes listed have the highest occurrence rating? This will indicate whether the FMEA team thought this cause was likely to happen or nearly impossible. Then we can look at what cause was listed under multiple failures. This would indicate that there could be a weak link with our product. We can start to narrow in on what could be the cause of our problem and then start doing some further investigations. We may be able to test product to verify a cause.
Dianna Deeney:In the FMEA controls column there should be a list of what prevention controls are in place, like machine settings. If there were prevention controls we can look into some manufacturing records to ensure those controls were functioning properly. Maybe we'll notice there was a non-routine maintenance performed on equipment that made the product. What was that about? Was it done properly or did it cause something to shift? Also, in the FMEA controls column there should be a list of detection controls in place, like inspections performed. Pull some of the records from quality assurance. Was there anything noted there? Were there defects found and what was done about it? Just from considering what someone is telling us is happening in the field, we can use an FMEA to help guide us to next steps for finding out the true culprit or root cause.
Dianna Deeney:Now, how much of a priority is this complaint? Do we need to recall product Again? this is where FMEA may help. This analysis was done during a time when there were cool heads. People were rational and realistic. When the FMEA was done, we can assume We can check its reports or notes for how the team made decisions about ratings. Was it the most likely, what was the most severe, and so on. So how bad is this complaint? Look up the ratings and how it was ranked in the FMEA. Does it still make sense?
Dianna Deeney:After the complaint is resolved, ensure you go back to the FMEA and make updates. After all, you've now made discoveries about the product. Your discovery might be that the information in the FMEA is still accurate and doesn't need to be changed, or you might discover that a failure-cause combination is happening more often. Or your team decided that the controls that we had in place, like machine settings or inspections, weren't good enough and you decided to add another control. Then you can add that control to the FMEA. Now, when the next new engineer is assigned to that product line, they'll have the FMEA to get started, just like you did.
Dianna Deeney:What's today's insight to action? We talked today about how to use an FMEA to help us investigate a field failure of our product. Having talked through this, my wish is that we see how we can also use it during development. I've seen a lot of posts on social networks about how the risk index is just outdated. It's the green-yellow-red matrix of severity and occurrence. Really, it's just one small way of evaluating FMEA data, and not even a necessary one. Your team may choose not to use it at all. You can use FMEA like we did today Evaluate the chain of events, examine causes, check controls, turn that information into knowledge and then innovate. If you like the content in this episode. Visit QualityDuringDesigncom, where you can subscribe to the weekly newsletter to keep in touch. This has been a production of Deeney Enterprises. Thanks for listening.